Enhancing Efficiency: Non-Sparking Wrenches for Seamless Operations
May 01,2025
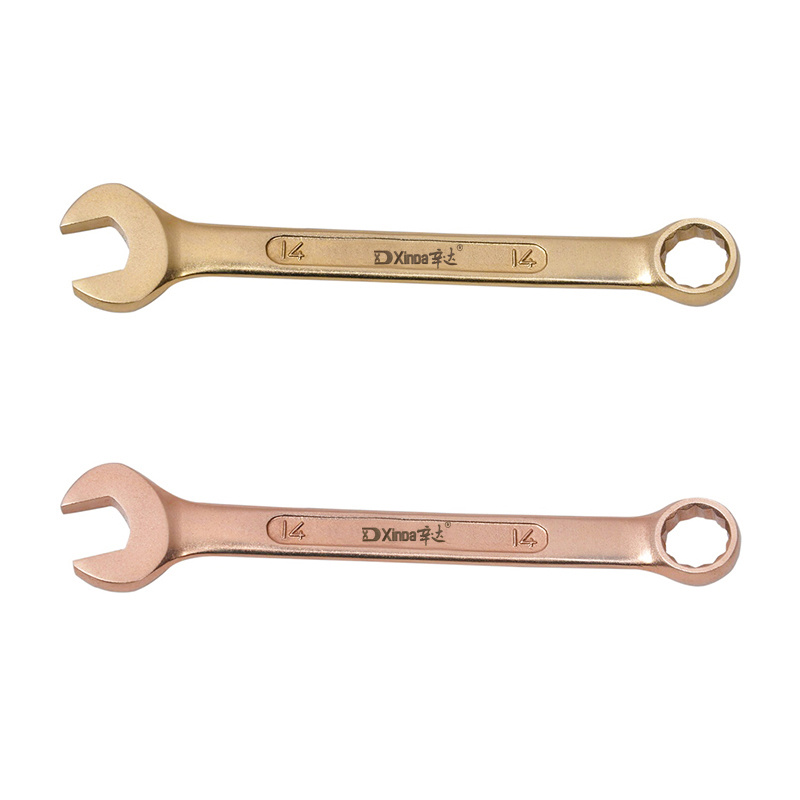
Enhancing Efficiency: Non-Sparking Wrenches for Seamless Operations
Table of Contents
- 1. Introduction to Non-Sparking Wrenches
- 2. Benefits of Using Non-Sparking Wrenches
- 3. Key Features of Non-Sparking Wrenches
- 4. Materials Used in Non-Sparking Wrenches
- 5. Applications of Non-Sparking Wrenches in Various Industries
- 6. Safety Considerations When Using Non-Sparking Tools
- 7. Maintenance Tips for Non-Sparking Wrenches
- 8. Conclusion
- 9. FAQs About Non-Sparking Wrenches
1. Introduction to Non-Sparking Wrenches
In industries where flammable gases, vapors, or dust are present, the risk of fire or explosion is a significant concern. To mitigate this risk, **non-sparking wrenches** have emerged as essential tools. These specialized tools are designed to prevent spark generation during operations, making them invaluable in hazardous environments. By enhancing operational efficiency and ensuring safety, non-sparking wrenches play a critical role in various industrial applications.
2. Benefits of Using Non-Sparking Wrenches
Non-sparking wrenches offer a multitude of advantages, particularly when safety is a priority. Below are some of the key benefits:
2.1 Enhanced Safety
The primary benefit of non-sparking wrenches is their ability to prevent ignition sources in explosive atmospheres. This feature significantly enhances the safety of workers and equipment.
2.2 Increased Productivity
By reducing the risk of accidents, non-sparking wrenches allow workers to focus on their tasks without the constant worry of creating sparks. This leads to smoother operations and increased productivity.
2.3 Longevity and Durability
Many non-sparking wrenches are made from high-quality materials that resist wear and tear. This durability translates to longer tool life, reducing the need for frequent replacements.
3. Key Features of Non-Sparking Wrenches
Understanding the features that distinguish non-sparking wrenches is crucial for selecting the right tools for specific applications.
3.1 Spark Resistance
Non-sparking wrenches are specifically engineered to avoid generating sparks, even under high-stress conditions.
3.2 Ergonomic Design
Many models come with an ergonomic design, ensuring comfort for prolonged use. This design reduces fatigue and improves grip, allowing for optimal performance.
3.3 Variety of Sizes and Types
Non-sparking wrenches are available in various sizes and types, including open-end, box-end, and adjustable wrenches, catering to a range of applications.
4. Materials Used in Non-Sparking Wrenches
The materials used in the construction of non-sparking wrenches are crucial for their performance and safety features. Common materials include:
4.1 Copper-Aluminum Alloys
Copper-aluminum alloys are widely used due to their excellent corrosion resistance and non-sparking properties. These alloys provide the necessary strength while maintaining lightweight characteristics.
4.2 Beryllium Copper
Beryllium copper is another popular choice for non-sparking tools. It is known for its high strength and hardness, making it suitable for heavy-duty applications.
4.3 Bronze
Bronze wrenches are also non-sparking, offering good corrosion resistance and durability, making them ideal for marine and chemical applications.
5. Applications of Non-Sparking Wrenches in Various Industries
Non-sparking wrenches find a variety of applications across different sectors, including:
5.1 Chemical Processing
In chemical plants, the risk of explosions from volatile substances is high. Non-sparking wrenches are essential for safely handling equipment in these environments.
5.2 Oil and Gas Industry
The oil and gas industry frequently deals with flammable materials. Non-sparking tools are critical for maintenance and operations to prevent accidents.
5.3 Mining Operations
In mining, where methane gas can accumulate, non-sparking wrenches are vital for safe equipment maintenance and repairs.
5.4 Aerospace Industry
The aerospace sector also relies on non-sparking tools, especially in maintenance operations involving fuel systems and other flammable materials.
6. Safety Considerations When Using Non-Sparking Tools
While non-sparking wrenches significantly enhance safety, users must adhere to specific guidelines to maximize safety.
6.1 Proper Training
Workers should receive adequate training on the proper use of non-sparking tools to avoid misuse that could lead to accidents.
6.2 Regular Inspections
Routine inspections of non-sparking wrenches are crucial to ensure they are in good working condition and free from damage.
6.3 correct Storage
Non-sparking wrenches should be stored in a dry place to prevent corrosion and maintain their non-sparking properties.
7. Maintenance Tips for Non-Sparking Wrenches
To ensure the longevity and performance of non-sparking wrenches, implementing proper maintenance practices is essential.
7.1 Cleaning After Use
After each use, clean the wrenches to remove any dirt or residue that could compromise their effectiveness.
7.2 Lubrication
Using an appropriate lubricant can prevent wear and tear, ensuring smooth operation for adjustable wrenches.
7.3 Avoiding Over-Tightening
Excessive force can damage non-sparking wrenches. Always use the appropriate torque settings to avoid unnecessary stress on the tools.
8. Conclusion
Non-sparking wrenches are indispensable tools in industries where safety is paramount. Their unique properties and features not only enhance operational efficiency but also protect workers from potential hazards. Understanding the materials, benefits, and proper maintenance practices associated with non-sparking wrenches can significantly impact productivity and safety in various applications. As industries continue to prioritize safety, investing in high-quality non-sparking wrenches is a step forward in ensuring seamless operations.
9. FAQs About Non-Sparking Wrenches
9.1 What are non-sparking wrenches made of?
Non-sparking wrenches are typically made from materials like copper-aluminum alloys, beryllium copper, or bronze, which are designed to prevent spark generation.
9.2 In which industries are non-sparking wrenches used?
Non-sparking wrenches are used in various industries, including chemical processing, oil and gas, mining, and aerospace, where flammable materials are present.
9.3 Are non-sparking wrenches more expensive than regular wrenches?
Generally, non-sparking wrenches may have a higher initial cost due to the materials used. However, their durability and safety benefits often justify the investment.
9.4 How do I maintain non-sparking wrenches?
To maintain non-sparking wrenches, clean them after use, lubricate when necessary, and avoid over-tightening to prevent damage.
9.5 Can non-sparking wrenches be used in all environments?
While non-sparking wrenches are designed for use in hazardous environments, they should still be used following appropriate safety guidelines and training.
TAG:
PREVIOUS:
Contact Us
E-mail :
info@xdtools.com
Phone/Wechat/WhatsApp:
+86-15830107628
Address:
Xinleitou Industry, Xinji City, Shijiazhuang City, Hebei Pro.,China.